Acceptable Quality Limit (AQL) is often viewed as the gold standard for quality assurance and quality control. It is indeed a powerful tool with many upsides. However, knowing how to use it – and when not to – can be challenging.
A guide to Acceptable Quality Limit (AQL) should start with underscoring its great usefulness throughout production environments. For quality in your supply chain, few tools are as useful as AQL.
AQL is, however, not the end-all or fix-all solution. It is a powerful part of companies’ quality assurance, quality control and audit setup, but it is not the only tool you should use.
In this introductory AQL guide, we will take a closer look at how and when to use AQL – when to consider using something else - and some of the most common questions surrounding the subject. In future articles, we will take a closer look ’under the hood’ of AQL and explore its uses in specific production environments and industries.
What is Acceptable Quality Limit?
AQL can be defined as a calculation of the bearable/acceptable quality level of a given production.
If you make or sell shoes, AQL defines how many pairs of sneakers out of a production batch of 10,000 you can accept having minor or major defects. If you make or sell shelving units, it can tell you how many out of 1,000 can have scratches.
To expand a bit: AQL is the industry sampling standard for consumer and industrial production. It represents the maximum tolerable defects in a production cycle for a specific party., calculated per ISO standard 2859-1. If a given production batch – or average for a series of batches – exceeds the contractually agreed upon AQL limit, it is rejected.
Product sellers, importers and producers will most often calculate AQL based on standardised tables using a series of categories that define the severity of identified errors, such as critical, major, and minor defects.
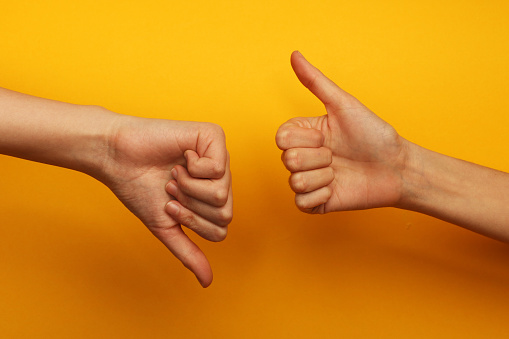
What is AQL Used For?
Producers and buyers often need agreed-upon industry standards for errors and defects. Otherwise, contract negotiations can get bogged down by QA and QC minutiae. Instead, parties can use the tables to specify acceptable quality levels of one or more production batches. For example, an AQL of 2.5% means there can be a maximum of 2.5% defects (of a specific category, but more on that later). This can be in a particular production batch or an average for several batches. A production contract should specify the steps following a batch exceeding the limit AQL limit.
Changes in AQL performance over time can be used as a yardstick to measure QA and QC initiatives’ efficiency and the effect of other upgrades on production processes.
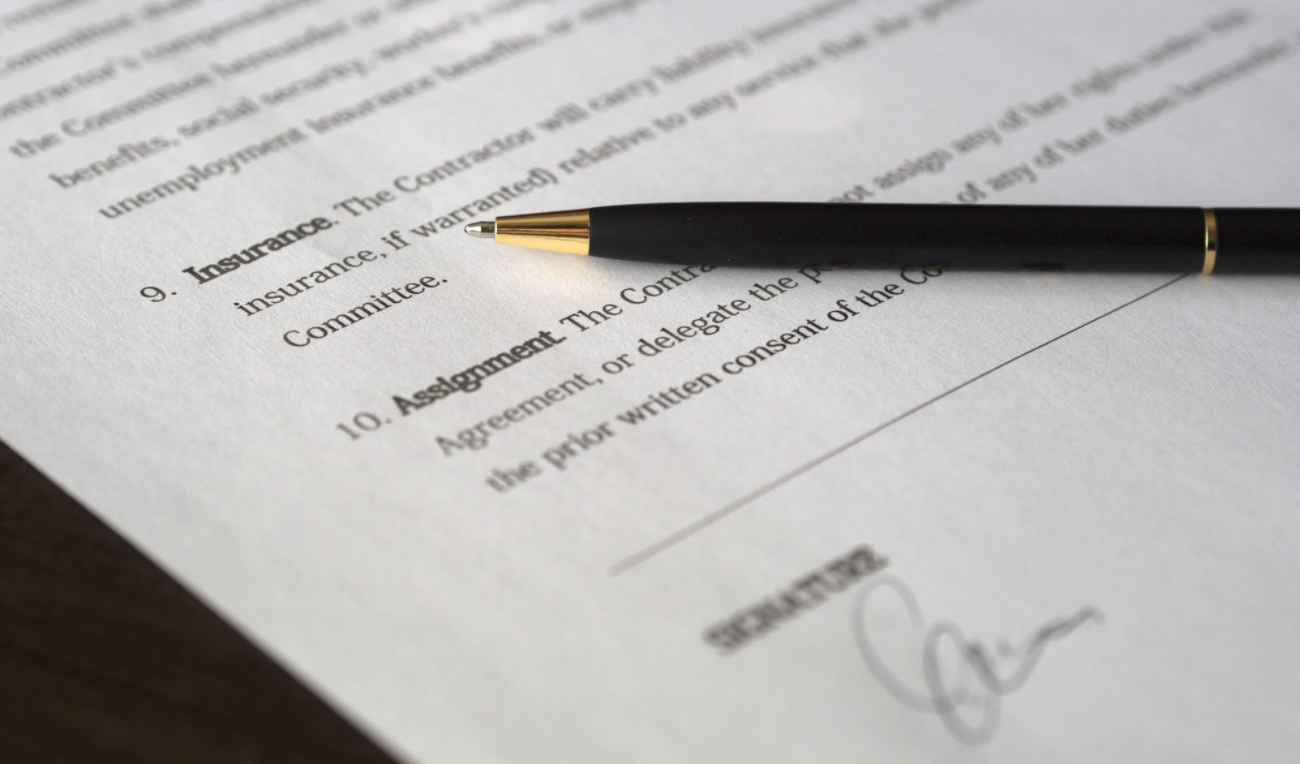
AQL Sampling Tables
The calculations required for generating your acceptable quality limit are often based on AQL sampling tables (see below).
Using the ANSI AQL charts below, you first find how many samples you should pick for inspection. Secondly, the tables show what number of samples can have errors if you set a given level for the percentage of defects you can accept.
If your contract says that AQL is 1%, then back-of-the-napkin calculations show that you can have up to 10 products with defects in a batch of 1000. If you have 11, the batch will be rejected. For reference, the number of defective products exceeding the AQL limit is often referred to as the Rejectable Quality Limit (RQL).
Checking all 1000 products is too time-consuming. Instead, you can use the AQL tables to determine how many you should select (sample) for quality control and the maximum number of defects allowable in the sample. This is calculated using statistic valid sample sizes.
How to read the AQL sampling tables
The first step toward making the best use of the AQL tables is knowing the core concepts and chart definitions.
Lot or batch size
How many units there are in a given production. If you, for example, are producing 8,000 pairs of shoes within one production cycle, then this is the batch size.
Inspection Level
Details what level of quality inspection you will carry out on the lot or batch in question. Inspection levels are often split in I, II and III – and categorised in general or special inspection levels.
Sample Size Code Letter
This letter is determined by lot/batch size and inspection level. If your production of 8,000 shoes will be checked at General Inspection Level II, the sample size code letter is ‘L.’
Sample Size
How many units in a batch will be selected for inspection. This can be found by looking at the second table. Find your sample size code letter, and you can see then umber next to it. For our example with the shoes, the letter ‘L’ shows that the sample size will be 200 units.
Acceptable Quality Levels
Details your AQL percentages – in other words, how many defects in the lot or batch are acceptable. If your level for the 200 units out of the 8,000 shoes selected as a sample is 1%, you can see the numbers ‘5’ and ’6’ in the Ac and Re columns. This means, if you can only accept up to 1% of your lot or batch to have defects, you will reject the shipment if you find more than five defects.
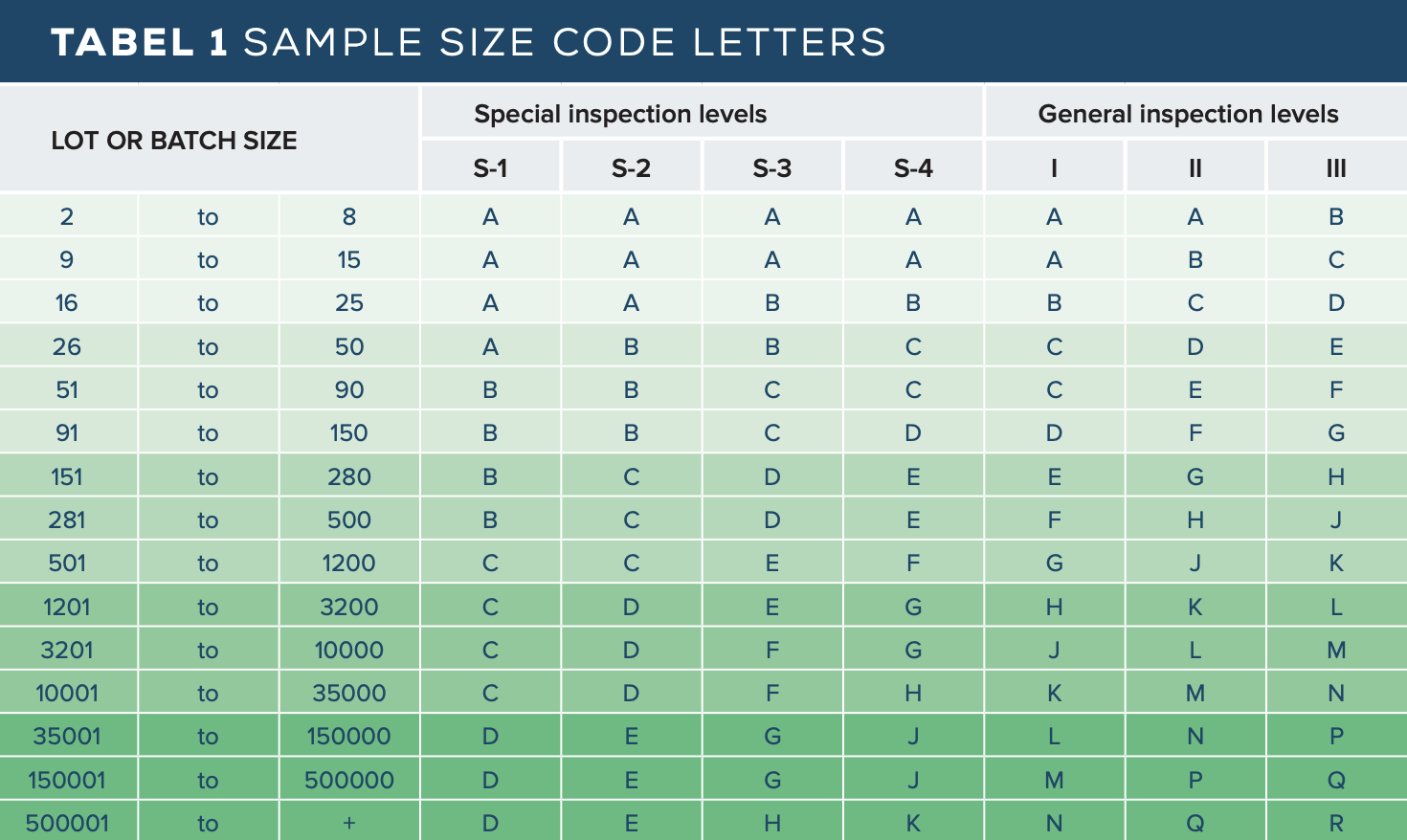
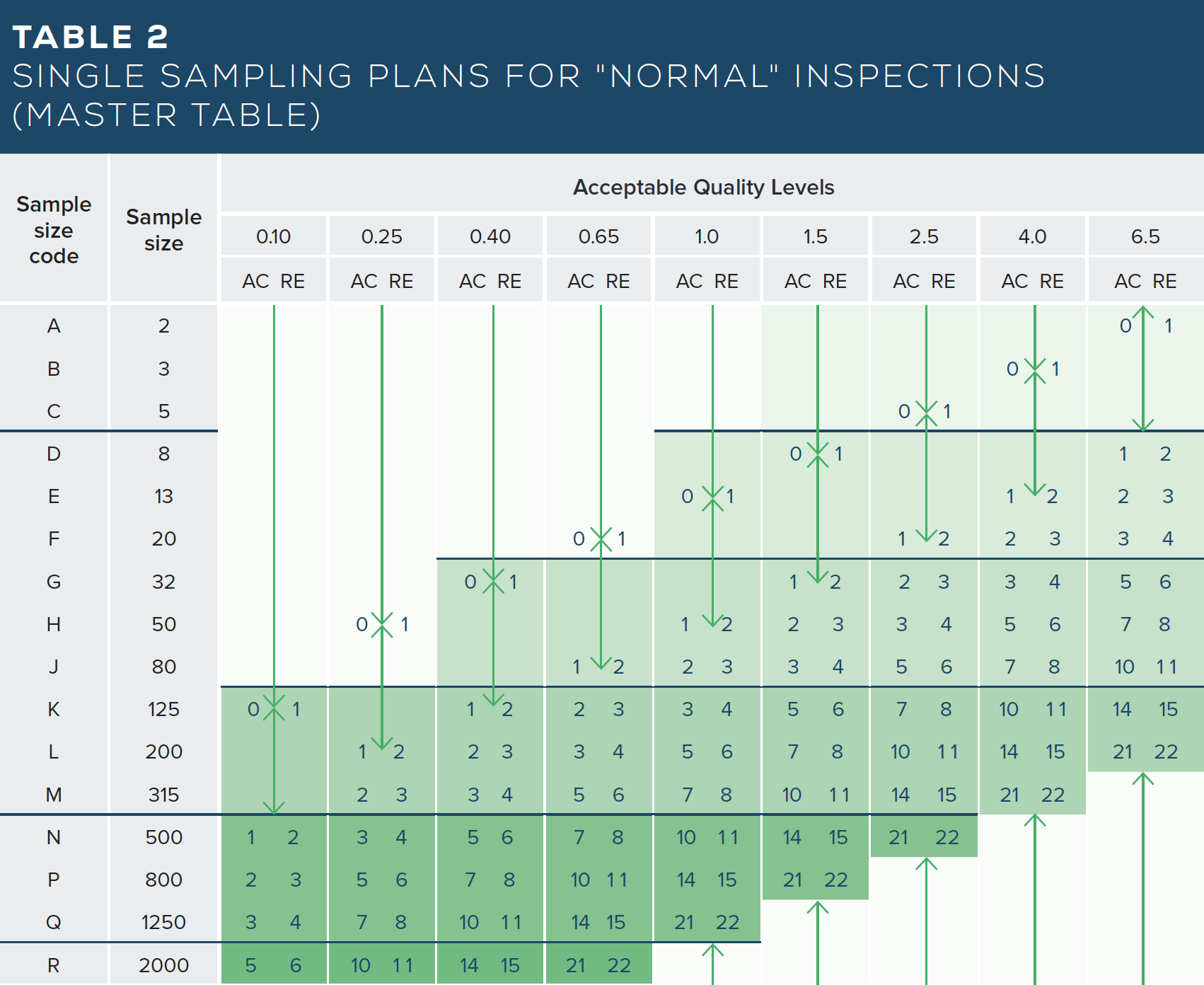

AQL Example 1
Company A orders 15,000 shirts from a clothing manufacturer in China. All shirts are produced in a single batch. Agreed-upon AQL levels are: 0.0% for critical defects, 2.5% for major defects, and 4.0% for minor defects. Inspection level is general inspection level II.
The first AQL table shows column and row-intersect is ‘M.’ In the second AQL table, M equals a 315-unit sample size for quality control inspection. AQL for critical defects is 0%, so the entire batch will be rejected if any are found.
M row intersection with the 2.5% column shows the numbers 14 and 15. The lower number, 14, represents the maximum number of allowable major defects. The intersection of row M and the 4.0% column shows 21 and 22, so if there are less than 22 minor defects, the entire batch will be accepted.
AQL Example 2
Company B orders a batch of 3000 office chairs from a manufacturer in Vietnam. Using the AQL tables, they identify that a General Inspection II code letter for the batch would be ‘K´.
Looking at the second table, the company finds that it needs to perform QC on 125 chairs. The company has set an AQL for critical defects at 0%, major defects at 1% and minor defects at 6.5%. After inspecting all 125, there must be no critical defects, a maximum of three major defects and a maximum of 14 minor defects for the batch to be accepted.
Qarma’s Top 3 Pieces of Advice
At Qarma we see over 1,000,000 QC inspections performed with our QC App every year. With AQL built directly into the app it's a native part for our customers but some areas we we always advise on to streamline their operations:
- Make sure your quality team aligns on defect severity: what counts as a major and minor defect must be clear to all involved parties.
- Ensure visual reporting of defects: One picture is worth more than 1000 words – also when considering AQL and QC.
- Select the sampling level according to risk exposure: Do not spend time on checking many units if there is little risk of errors.
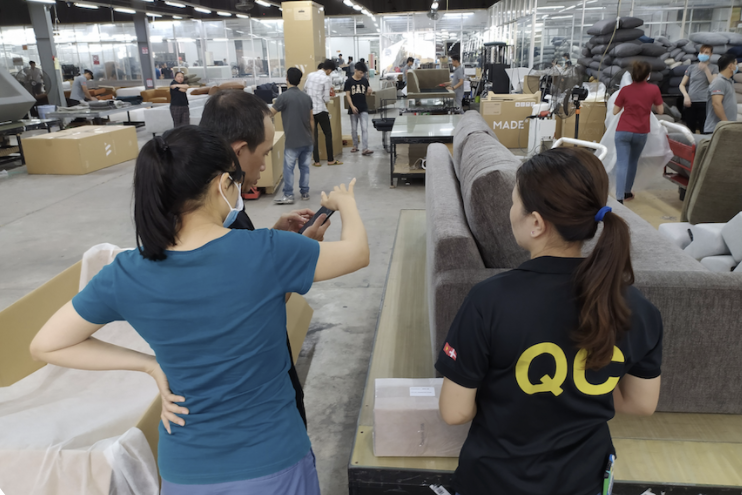
Frequently Asked AQL Questions
How do I use AQL in my specific business?
On the surface, it may seem that you already know the answer to that from the previous segment, right? However, you need to consider some crucial details about AQL.
One revolves around what is being produced. A scratch on the top of an eight-foot-high shelving unit is often a minor issue that very few people will ever notice – or care about. A similar small scratch in the top of a table is much more egregious. In other words, defining the severity of errors is pivotal for AQL success.
When you carry out your AQL inspection may also be defined by your products. For example, it is often not feasible to do AQL testing on products like office chairs before getting to the final stage after everything is packed.
Another area to consider is your brand value proposition. If you are a high-end brand, errors and mistakes in shipments can have an immense reputational impact – less so for brands focused on low-cost items.
Are There AQL Rules of Thumb?
Some AQL rules of thumb exist but often have to be fitted to your industry. It is heavily dependent on your product, market audience and use. Medical equipment is a good example of a space with very low AQL limits, whereas ballpoint pen production will likely have higher error and defect limits.
However, some AQL numbers and definitions are often used as contract standards:
Critical defects: This category of defects make a product either unusable or may put a user at risk of harm. Companies and importers generally set the AQL for critical defects at 0.0. In other words, finding one critical defect in a sample means that the entire batch fails inspection.
Major defects: While not as grievous as critical defects, major defects are still unacceptable for users. They are often described as defects that increase the risk of product failure before it should be expected. An AQL of 2.5% is often used for major defects.
Minor Defects: These are minor defects and errors that have low to no influence on product safety and usability. Many companies and importers will set a standard of a 4% AQL for this category of defects.
What Happens if an AQL Limit is Exceeded?
That will depend on what a given contract dictates. In almost all cases, the producer or subcontractor will be tasked with remedying the situation at their own costs. One way of doing that is to produce a new batch that hopefully meets AQL standards.
In cases with high production costs, the producer will likely survey every individual product and set aside those that meet the quality demands. A new batch for the remaining products is then produced.
If the individual product productions costs are low and quality inspection costs for every product is high, the batch will likely be scrapped or recycled.
What are AQL Pain Points and Challenges?
One of the core issues with AQL is defining what constitutes critical, major and minor errors. This will very likely depend on the nature of a given product – and varying industry standards. These are subjects we hope to look closer at in several follow-up articles.
Finding common ground and alignment may be a question of several iterations and debates and having such debates post-production can be difficult. A real-time QA and QC digital tool may help mitigate some of these issues and streamline communication about errors and how to fix them, especially if accompanied by high-resolution pictures and video.
AQL is focused on finished products. Once you spot mistakes, there may be no other option than to start the production process all over again. Carrying out dynamic controls and checks is advisable – as is looking at AQL as only part of your QA and QC processes that should also include line checks, etc.
AQL can, depending on your setup, require a lot of staff for inspections - especially if you are using complicated tools. Imagine that you have up to 100 subcontractors. If you have 10, or even 20, inspectors, you may not be able to cover every production line constantly. Instead, you can train and develop suppliers to carry out selected quality inspections themselves, which would free up resources for your own team to focus on the high-risk products. To properly monitor and manage a supplier self-QC program, it is recommended to use a digital tool to track and capture data on quality inspections.
Conclusion
AQL is a key aspect of operations when it comes to quality control. Figuring out your threshold and standardizing QC inspections based on agreed-upon levels and processes is pivotal for success.
Whether you are printing out the tables above or using a digital inspection app with built-in AQL calculations such as Qarma, having AQL as part of your toolkit will help you in your quality journey.