For Nick Green, owner of Teemo and second-generation leader of the family business, design has always been at the core of what he does. Growing up he saw firsthand how creativity could be turned into a career. Today, Teemo has been in business for 44 years, built around the idea of delivering aesthetic, high-quality designs at an affordable price.
Beyond aesthetics, Teemo believes that quality and responsibility go hand in hand, which is why they needed a system that could support their high standards and long-term vision.
A smarter way to work with Quality
At Teemo, every product must meet outlined quality criteria. Nick wants customers to love their pieces for years to come, which means ensuring consistent quality at every step of the process. When the company started working with Qarma, the goal was to move from traditional reporting methods to a more efficient, data-driven system that provided better insight and transparency. In short, make the quality last as long as the design.
“The fact that Qarma is cloud-based and real-time is a game changer. We can instantly access photos, click on them for greater details, and share them with customers and teams. That level of visibility is invaluable”, Nick explains.
Another key feature that stood out was the Power BI integration. By turning quality data into visual graphs and reports, the entire team – from factory staff to leadership – could engage with the data in a way that was easy to understand and act upon.
“Most people are visual, and when they see the data presented in a clear and interactive way, it makes a real impact,” says Nick. “If you don’t measure it, you can’t improve it – and that’s invaluable.”
What gets measured gets improved
Having access to real-time data has completely changed how Teemo approaches quality control. Instead of relying on static reports, the team now walks into factory meetings with visual presentations, showing tendencies, failure rates, and areas for improvement.
“If we ever have a small quality issue with a customer, we can go back, look at the photos, and pinpoint exactly where the issue happened,” Nick explains. “Sometimes, it’s not production – it could be a packaging issue. Having that level of insight helps us improve, not just react.”
To improve quality, it’s all about shifting the mindset to report all defects and findings, allowing data to drive real improvements. By documenting even minor issues, Teemo gains a clear overview of product consistency and factory performance.
Teemo actively uses data to refine their processes, reduce failure rates, and enhance overall quality. “The factory owners love it. They see the improvements and are motivated to improve and create consistent products,” says Nick.
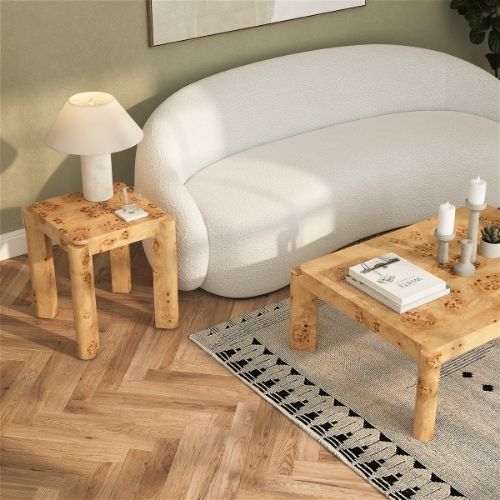
Efficiency that lets the team focus on quality
Before Qarma, Teemo’s quality team spent long hours manually compiling reports and pasting images into spreadsheets. This wasn’t just time-consuming – it took them away from their core job of ensuring quality.
Now, as inspections happen, reports are automatically generated, with photos and data seamlessly recorded. The switch has saved the quality team up to four hours a day – time that is now spent on improving product and processes rather than formatting reports.
“The quality team is there to check quality, not to create reports. The fact that Qarma does both at the same time is a no-brainer”, says Nick.
Quality is never static
For Teemo, quality is never static – it’s something to improve on every single day. The company has developed its own internal quality documentation to ensure every team member understands expectations, processes, and the level of detail required. Pairing this structure with the right technology has helped elevate their quality control to new heights.
As for the future, Nick sees no limit to how much they can refine their approach. “I just want to keep making better and better products. Every day, I want our designs to look better, feel better, and be more consistent. With Qarma, we have the tools to make that happen.”