Company overview
Founded in 1952 in Denmark, BoConcept has grown to an internationally recognised retail lifestyle brand.
The company produces a wide array of Danish design products for living spaces, offices, and outdoor environments based on the principles that have made Danish designed admired around the world. Simplicity, good craftsmanship, elegant functionality, and quality materials.
Today, the company has stores in 65 countries spanning six continents.

Growing at two speeds
Success comes with its own challenges. For example, rapid growth almost invariably creates new needs like evolving business processes to match increasing sales and revenue figures. Make no mistake, this is a good challenge to have – but a challenge, nonetheless.
“Turning challenges into new opportunities is core to our business - also when it comes to QA. With Qarma, we are at the forefront of industry developments. Together, we have been able to slipstream rapid growth and achieve a deeper quality understanding and conversation across every part of the supply chain,”
- Torben Blindbæk, Quality Manager at BoConcept
Torben Blindbæk points to how changes in the current supply chain climate have created industry-wide needs to swiftly align internal processes with changing market conditions.
In comparison, a classic QC setup makes maintaining consistency throughout production environments challenging. Broad supply chain networks help mitigate the impact of disruptive events like COVID-19 and enable broad conversations about quality. However, creating a joint understanding and definition of supply chain functions, structures, and how to best ensure quality can be difficult with traditional QA solutions.
Furthermore, traditional approaches can be time-consuming. Cumbersome Excel spreadsheets, and difficulties uploading images and reports on-site can exacerbate such issues. It also leads to a lag throughout the whole QA process.
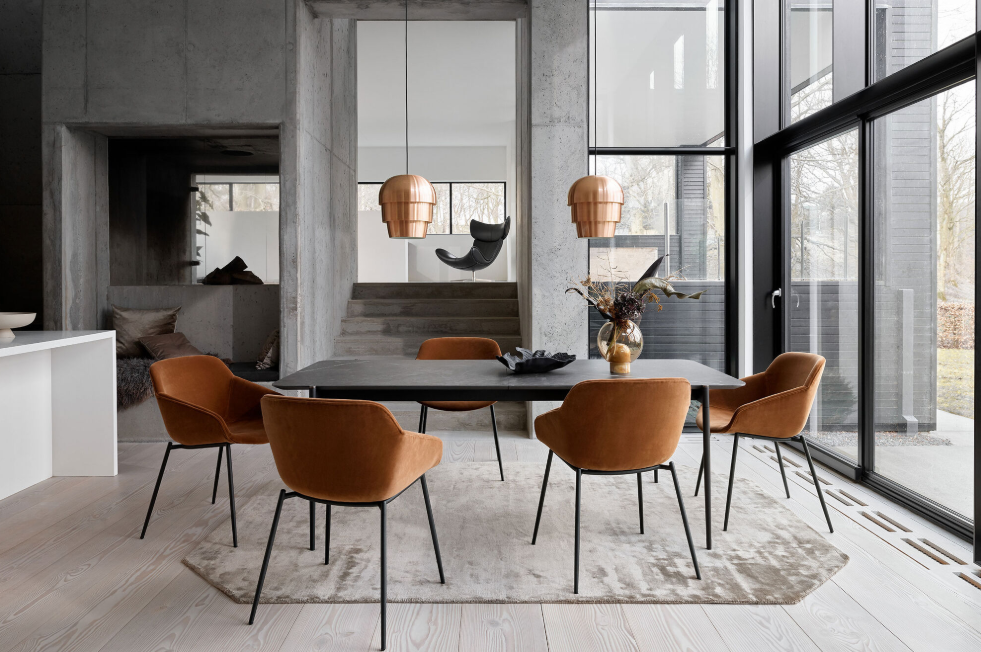
Implementing a quality journey
Improving real-time QC and QA communication was one of the parameters guiding BoConcept’s desire to expand its quality setup. Another factor was increasing transparency throughout the quality chain.
The goal was to turn traditional QA on its head and enable all involved parties to communicate and collaborate freely on improving quality.
“The vision is open communication and insight about quality across every step of the product’s journey. QA should reach from the production line into a customer’s living room, if you like. Qarma is a partner and tool that supports our approach and opens new opportunities for our quality controllers, in-house staff, and store managers”
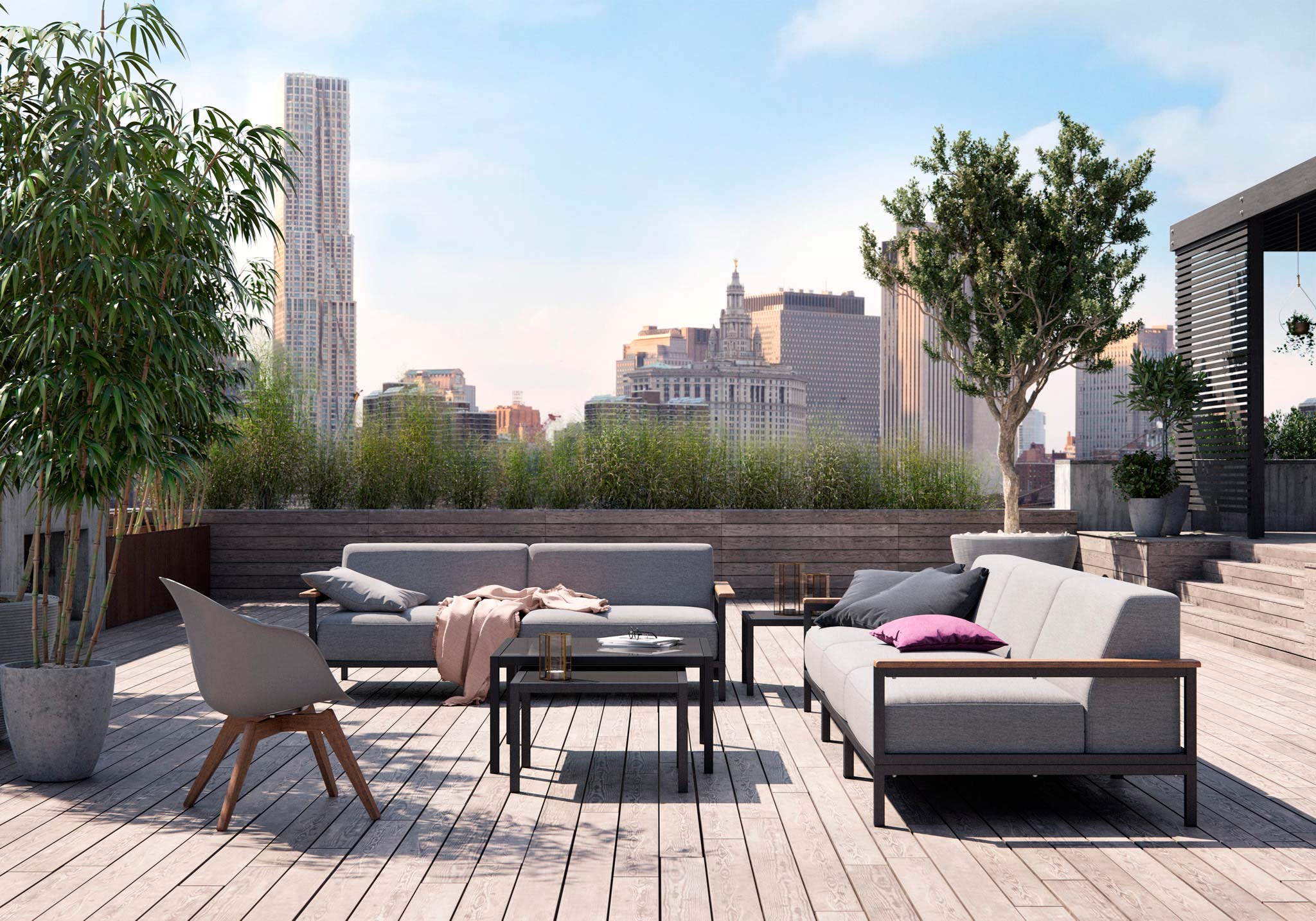
Removing IT from the equation
Going with Qarma was also influenced by its solution’s ease of use, ability to generate new insights, and automation features. From the first meeting, Torben Blindbæk was impressed with Qarma’s client connection approach and ability to tailor its solution to match clients’ needs. Furthermore, early-stage support, coaching, and training helped make Qarma an instant success.
Finally, Qarma’s flexible services and scalable pay-as-you-go pricing model provided the elasticity BoConcept was looking for throughout the QA setup.
“QA can be susceptible to technological bottlenecks. With Qarma, you have a solution that simply works. That was the exact message we got from our 14 on-site quality controllers within minutes of them starting to use it during an initial pilot project”

Results
For BoConcept, the introduction of Qarma has helped save resources and quality controllers’ time. This time has been redeployed elsewhere to increase QA and QC effectiveness. Furthermore, it has enabled quality controllers to work proactively with manufacturers on developing their internal QC efforts and upgrading production techniques to ensure quality.
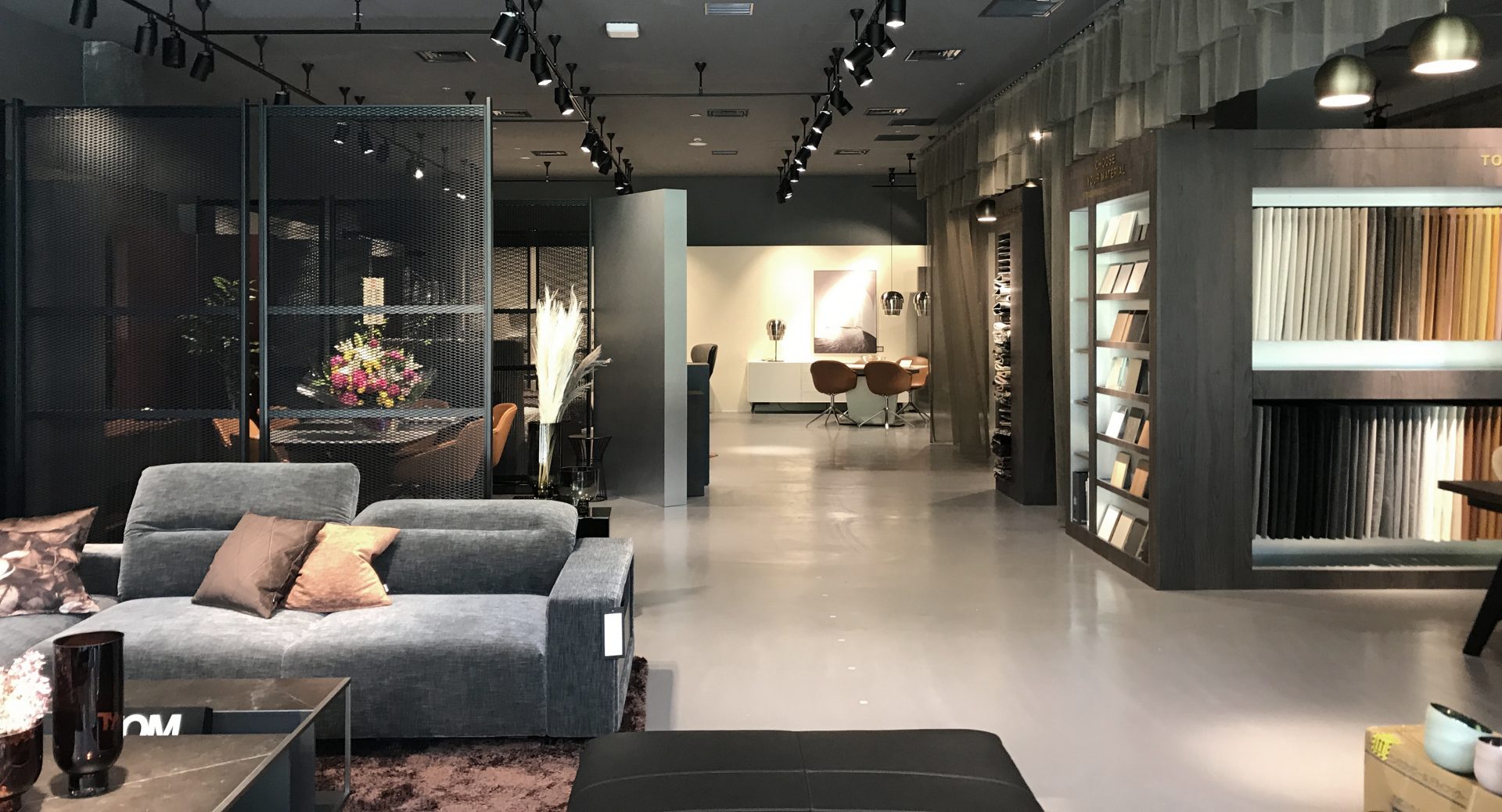
Internally, Torben Blindsbæk and his quality management team have used the changes to increase communication volume and speed. Qarma’s automatically generated reports have been core to freeing up time and increasing understanding of QC and QA throughout the organisation.
Qarma’s tools and collaboration has been pivotal for BoConcept developing a new mindset around quality and quality control. The approach is markedly different from the traditional QA view with static reports that is still pervasive in some parts of the furniture and design manufacturing space. Instead, BoConcept works with a dynamic Quality Journey for any given product.
“With Qarma, we have a better way of engaging with suppliers and collaborators. We can see images of any reported defects or errors when and where they occur. On the factory floor, that helps us identify what may have caused defects and immediately correct the issue. The same dynamic applies all the way into our stores”
“Internally, Qarma helps increase understanding and appreciation of our quality efforts. Instead of the classic QA and QC approach, which was more static and perhaps compliance-focused, we now have a Quality Journey. This is an approach where QA and QC is embedded in every step the product takes – and invites people to take part throughout that journey.”
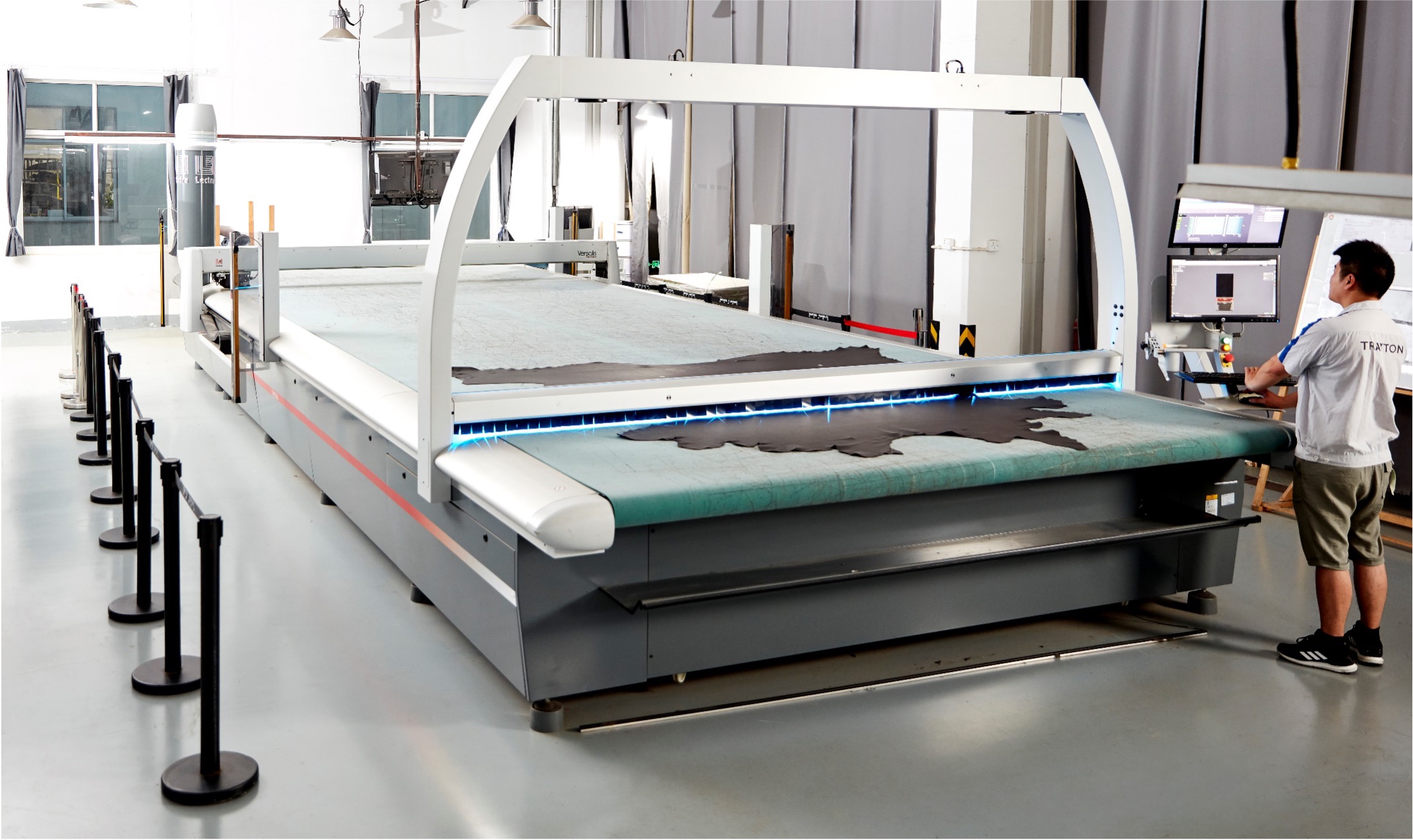